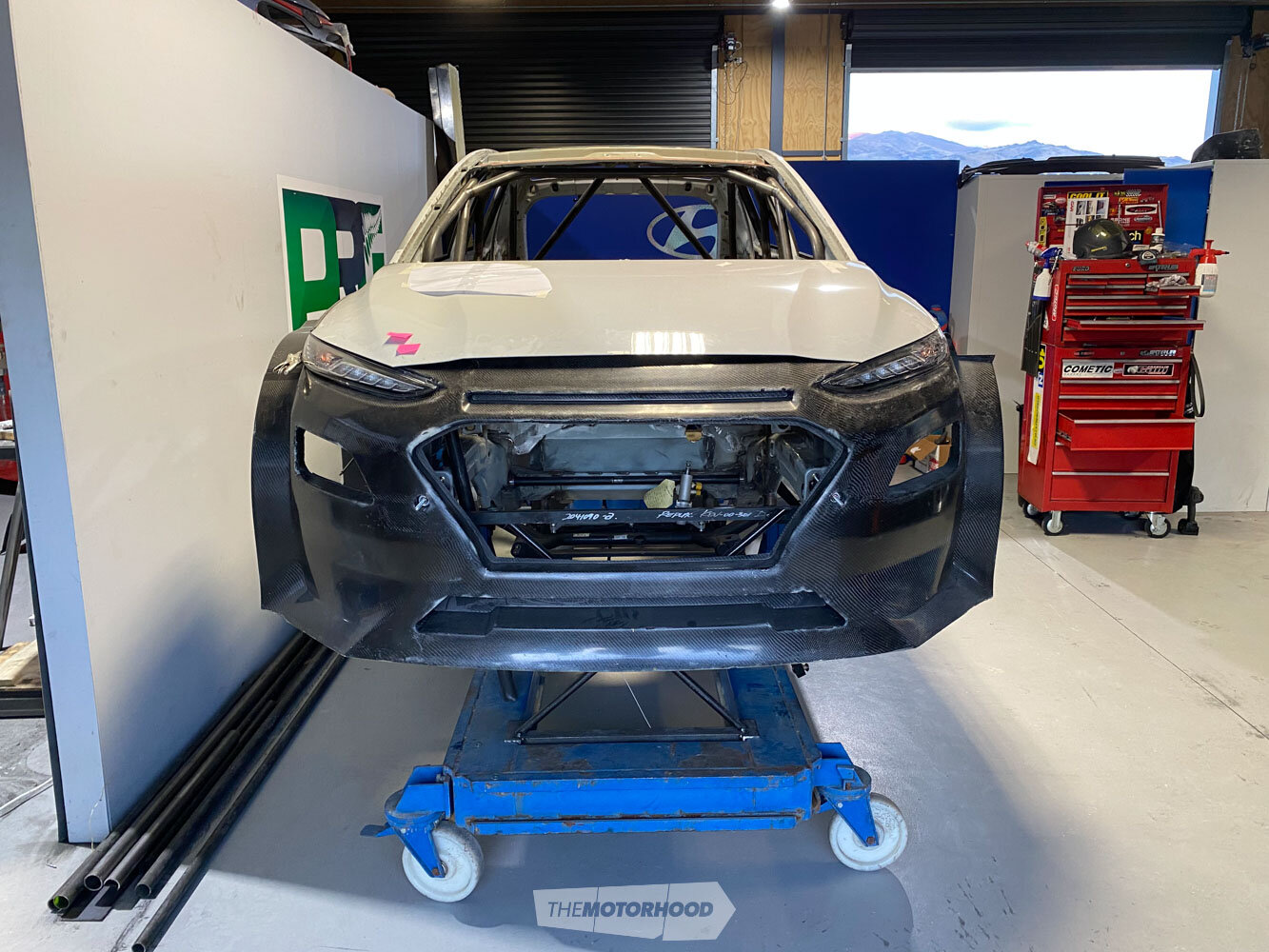
Despite the craziness in the world of late, everyone is now back on deck at Paddon Rallysport, with plenty of progress being made to the Hyundai Kona EV Rally car.
Prior to the lockdown, there was a big push in the workshop with the build and fabrication of the chassis. Despite the five-week delay, immediately after lockdown we were able to get the chassis to a point where we have now been able to start dummy-fitting parts and engineering the next steps of the process, such as mountings and location of components.
The chassis build was a long process. After over 600 hours of engineering time, it is now 90 per cent of the way towards completion. The changes we’ve had to make include the roll cage, a new rear floor pan (to clear the rear drivetrain, which sits underneath), a new main floor (complete with the mounting frame for the battery), modified front and rear shock mounts, modified subframe mounts, and lightening the body shell as much as possible.
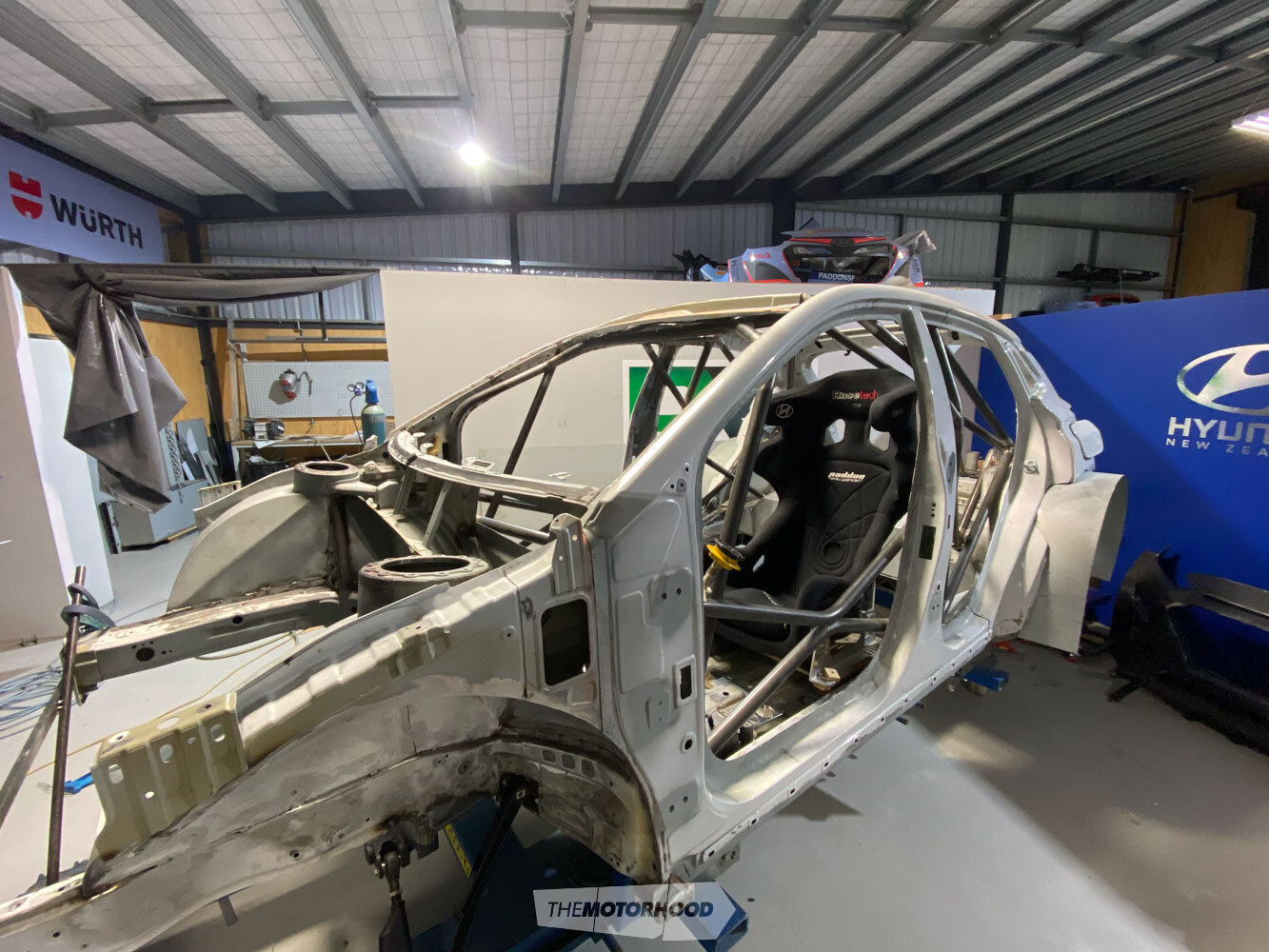
Now with the bulk of the chassis fabrication done, we have begun to dummy-fit the carbon body kit (developed in collaboration with the University of Canterbury) along with subframes, steering rack, and suspension arms. We have had most of the sub-assembly parts in place for several months, so the next steps of the project are expected to happen quite quickly.
Due to the current global situation, our technical partners STARD and EXT Suspension were delayed in sending our custom battery and suspension package. These components are now on their way. In the meantime, we have constructed a dummy battery based on our CAD model which will allow us to continue moving forward with all the mounting of components in the car. Waiting on some of our components has also given us time to start learning and developing the MoTeC software further, which will control the power distribution, motor and battery control, and torque vectoring. The MoTeC hardware and software will play a pivotal part as the ‘brain’ of the car.
As the Kona is a bigger car, this means that we have to mount the seats and pedal boxes higher in it to give the driver good visibility. This gives us the opportunity to mount components under the seats and utilize the floor to keep the bulk of the weight as low as possible. While the initial car will be heavier than your traditional car, the centre of gravity and centre of mass will be very low and central. There is no overhanging weight over the axles, with 90 per cent of the car’s weight contained between the axles.
With the way car manufacturers are going, we expect small SUV class vehicles (such as the Kona) will be adapted into rallying more and more. It’s a vehicle that has more commercial relevance for manufacturers and, in the case of our project, it gives us more space for increased battery capacity and mounting components that we wouldn’t normally have in a smaller car. With the design of the suspension and subframes, the car will not sit high like a SUV — its relevance to the ground will be the same as a current rally car. Just being taller and wider in the body dimensions means it will look bigger on the road, but the development of our aero kit will bring it in line with a current/modern-looking WRC car.
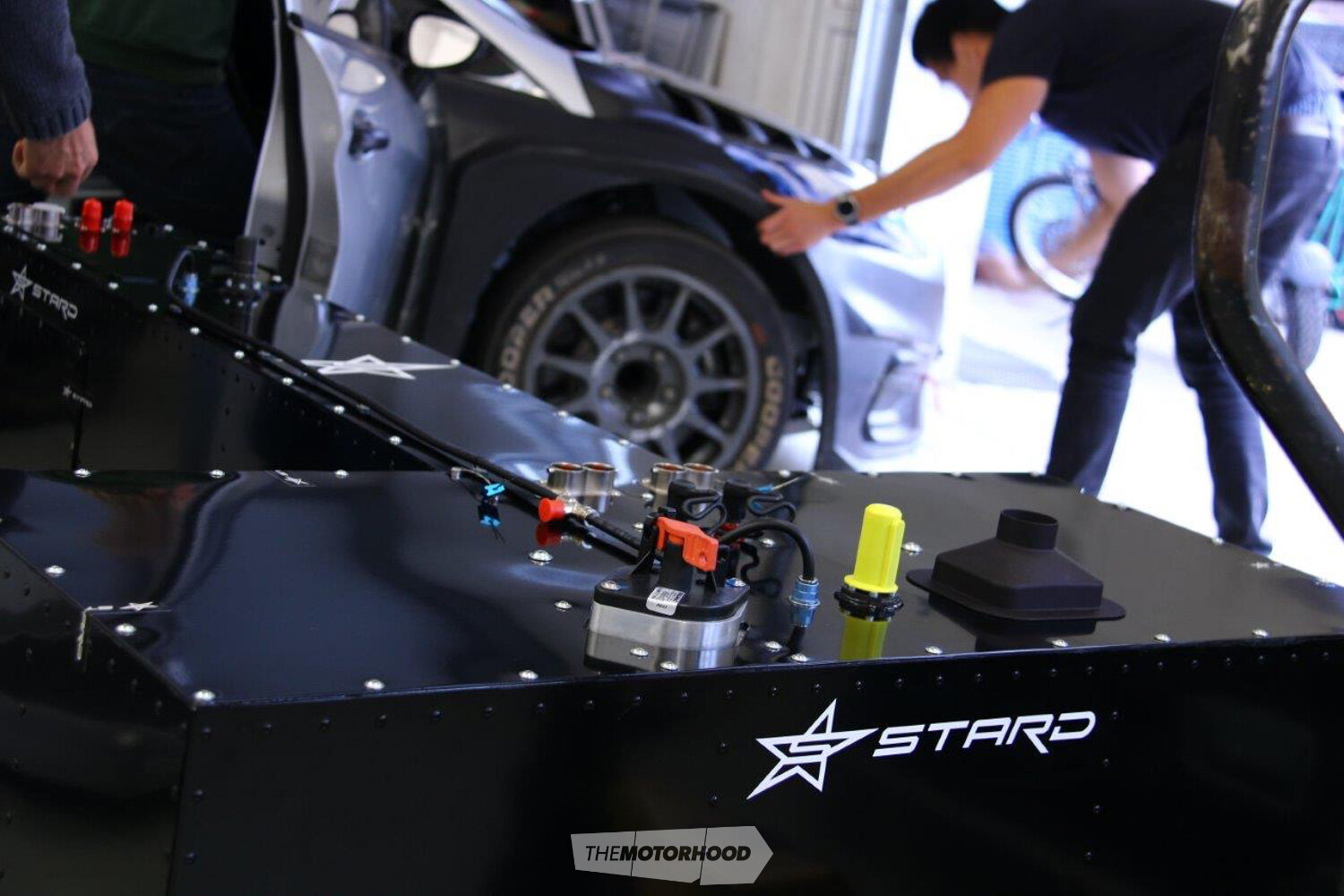
With all the delays and shortage of events, our deadline date has now been pushed to later in the year. However, we are looking to have the car mobile in the coming months and the final product released during August–September. There’s still a lot of work ahead for the engineers and technicians, but we are excited that it is now looking like a car and we are getting closer to the first ‘roll-out’.