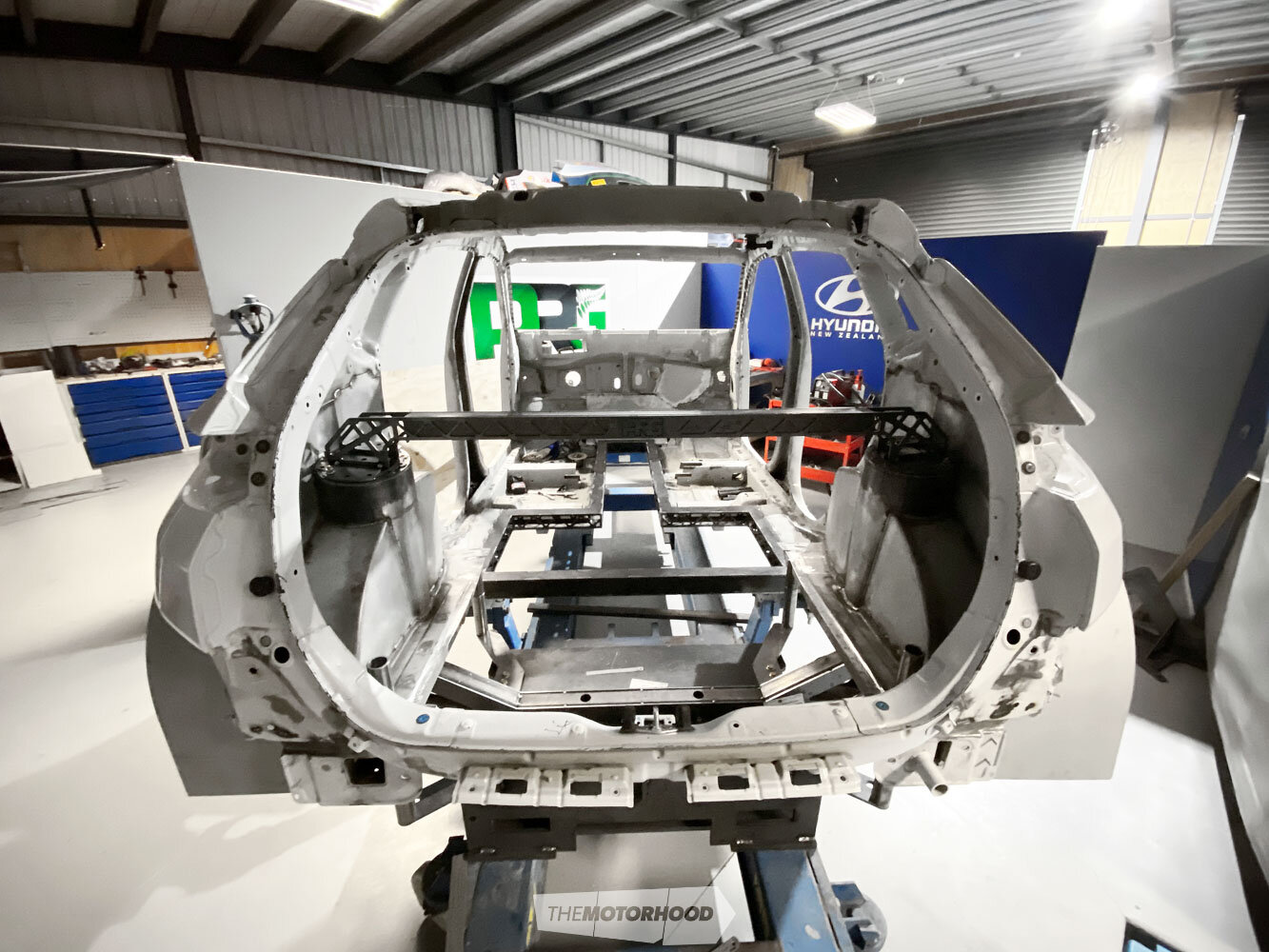
The months are sure whizzing by as our May / June deadline looms closer. With each passing day, progress on the EV rally car is ramping up as the chassis build nears its completion.
The construction of the chassis involved 10 months of design work. After the initial concept was devised, we had to analyze every aspect with excruciating detail. Countless hours were spent simulating suspension concepts, taking into account a considerably different weight distribution, to refine each critical pickup point — once these are installed on the car, there is no going back.
Packaging every component inside the chassis proved to be an equally time-consuming and technical challenge. The biggest nightmare was the rechargeable energy storage system (RESS) — the battery along with its auxiliary systems. The dimensions of a RESS are more or less restricted to discrete rectangular blocks, or modules, so that reduces the packaging flexibility — whereas a fuel tank can be moulded to almost any shape. Add to this the fact that we need at least 10 times the volume of batteries to meet the same energy storage of E85, and even with the generous space of the Hyundai Kona, we had a challenge on our hands! Safe to say that, after multiple revisions, everything fits, albeit rather snugly.
With the suspension top mounts (to allow for the massive 255mm of suspension travel), suspension pickup points, subframe mounting points, RESS mounting frame — which is also the replacement for the floor — and most of the roll cage in place, we are nearly at the point of being able to bolt the major components to the car. However, it’s a matter of one step forward, two back, and so forth while we carefully go through every step.
Once the car is semi-assembled, it will be fully dismantled to confirm and validate all designs and fitments, and overall operation, before we begin to fine-tune it and add the finishing touches of paint and body work. In fact, paint will be one of the last things to be done to the car.
Once the major components are dummy fitted in the car, the fun bit comes: marrying everything together. Apart from the transmission, RESS, and inverters, everything is being designed and built in-house. That means every suspension component, mounting bracket, wiring harness, safety device, and so on. This is a massive job for our team of engineers, who have already designed more than 1000 individual parts, from small spacers to suspension damper casings and roll cages. Designing and building a car from scratch with very limited off-the-shelf parts is certainly a challenging but exciting project, on which, although pressure is mounting, everyone is thriving.
Over the next month the car will start to look less like a bare shell and more like a car — especially once we take delivery of the new aero kit, which we have developed in conjunction with the University of Canterbury, which is currently manufacturing all the moulds.
T — minus 3 months!
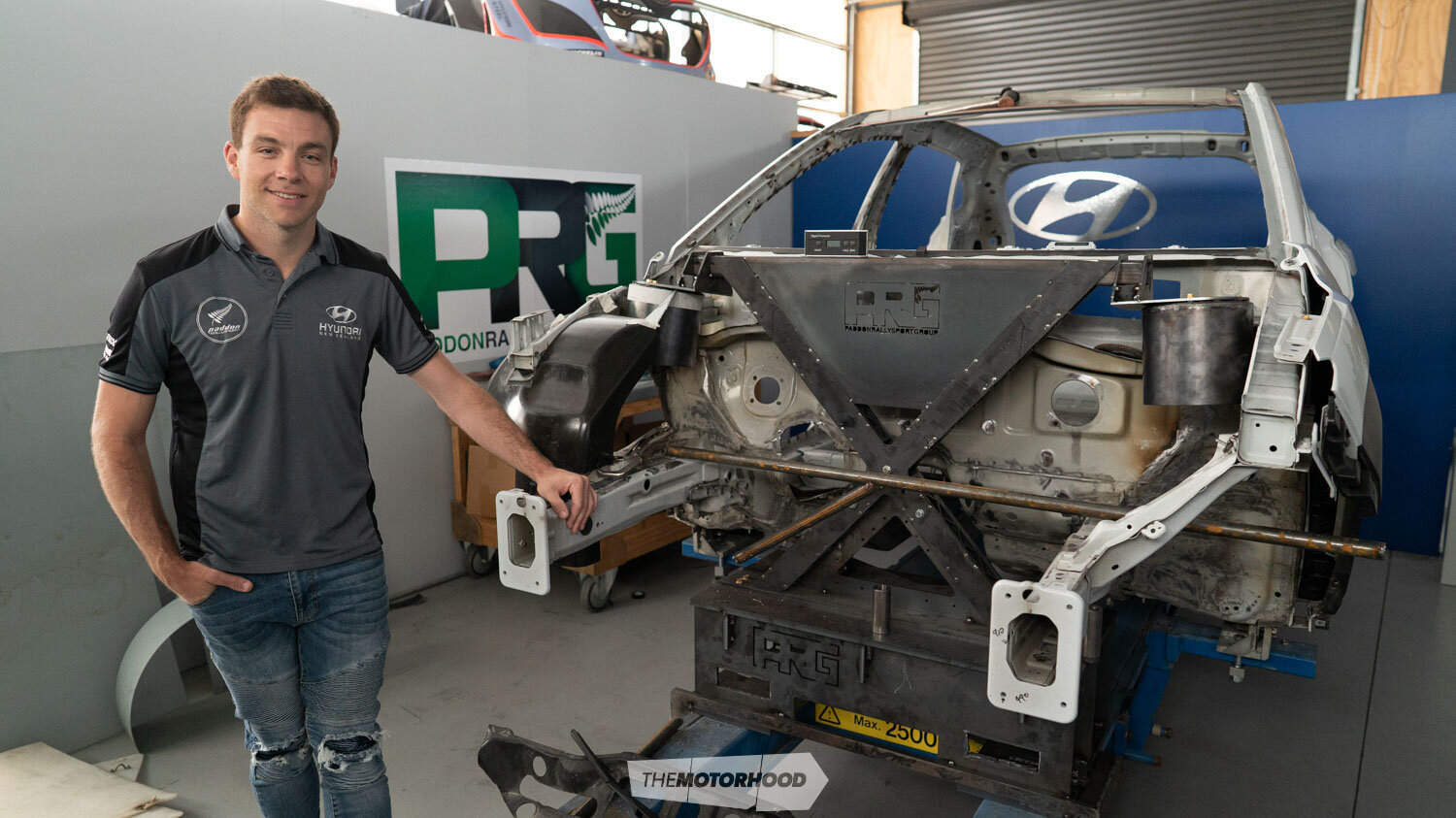