Most of us will have stood alongside a drag strip and watched 1000s of horsepower transfer through a set of big black slicks, which twist up and propel the car forward with an aggressive amount of force. But did you ever stop to think about how those tyres were made?
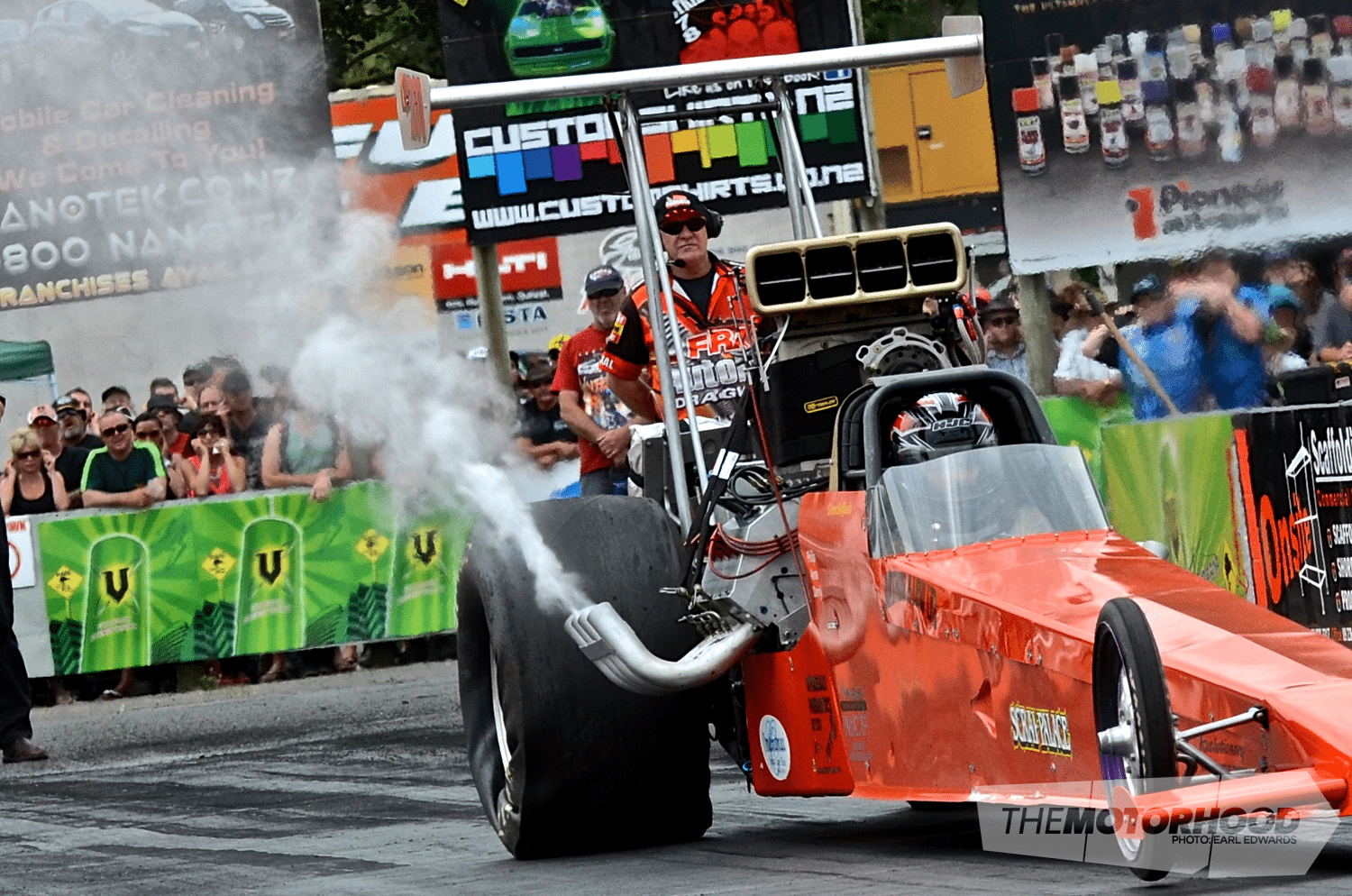
In the Top Fuel category, the tyre will go from a 36-inch diameter to 44-inch by the run’s end and instantly back to 36 once the throttle has been lifted — they are clearly not your run-of-the-mill steel-belted commuter rubber bands. So how do bias-ply slicks remain round enough to roll, yet deform so much during a drag run?
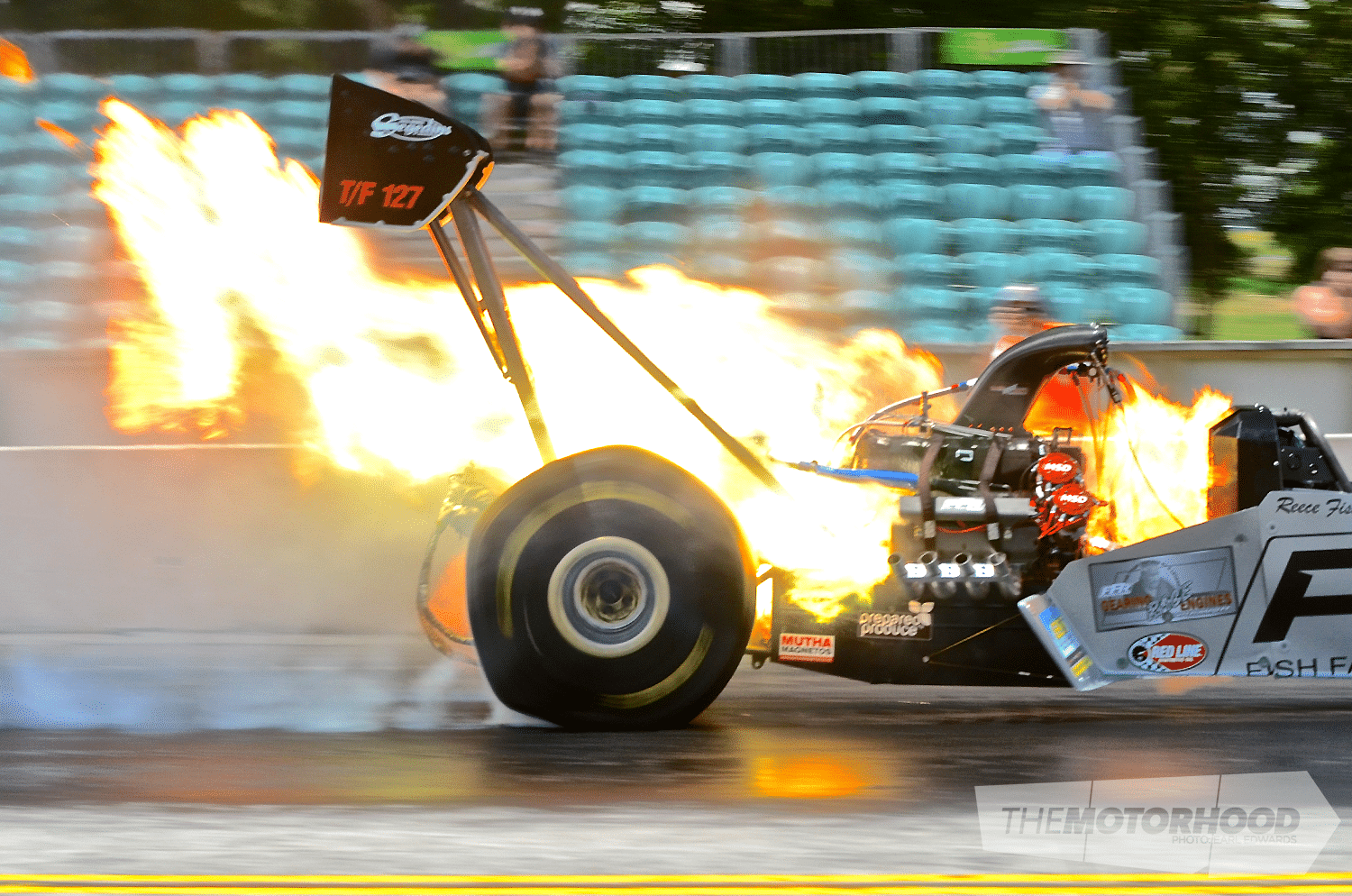
Take a look into the Goodyear factory to see the birth of a 300mph tyre; the video might be slightly ’90s-looking and lo-res, but it’s interesting none the less. Who would have thought that these things are hand-rolled like the finest Cuban cigar.
No points for guessing why these tyres need replacing so damn often. This is thanks to the pre-stage burnout, a key part of any drag run, and another point of the run where you can witness the tyre drastically changing shape.
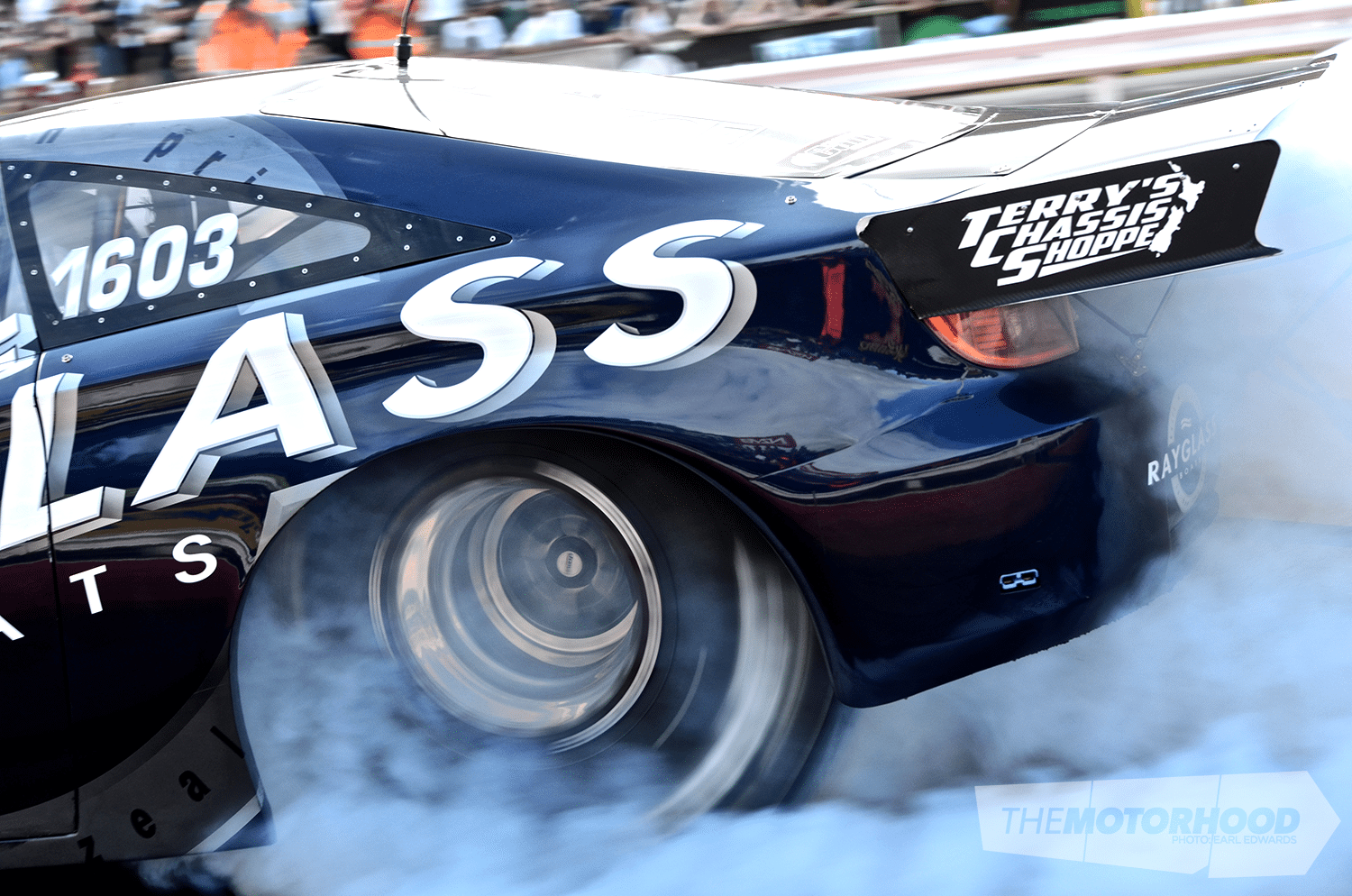